Years ago, we promised to repair or rebuild any make or model of gearbox to equal or better quality than original. Since then, we’ve kept that promise by bringing all important steps of the gearbox manufacturing process in-house under our control. This has entailed continuing investments in our footprint, our equipment and our people. We entered 2025 with major investments in all three.
In this article, we’d like to share some of these investments with you — all of which we made to serve you better.
Expanded footprint.
We started the year by expanding our operation into our new 10,000 square-foot shop addition. Our facility now encompasses a total of 44,000 square feet, with 5,000 square feet for offices and 39,000 for manufacturing.
“Our original building was 7,500 square feet for manufacturing and 2,500 for offices,” said Craig Massa, VP-Sales, “and we thought we wouldn’t need any more space.”
The addition had actually been planned since 2019 but was delayed by the COVID shutdown and licensing delays due to the building boom that followed.
This added space gives us room for the new CNC lathes, gear grinders and other large milling machines we’ve added. It also gives us separate space for refinishing and painting and for storing and keeping on hand replacement parts that will help us serve you faster. It also improves our workflow while enabling us to maintain our open, bright shop environment even as we grow.
Advanced technology.
Into our expanded footprint, we’ve added some of the most advanced gear cutting, grinding and checking machines in the world. Our shop now boasts four Kapp Niles gear profile grinding machines, including the KNG 12P and ZP 24, which weighs more than 22 tons and can handle gears up to 94.5” (2,400 mm) in diameter.
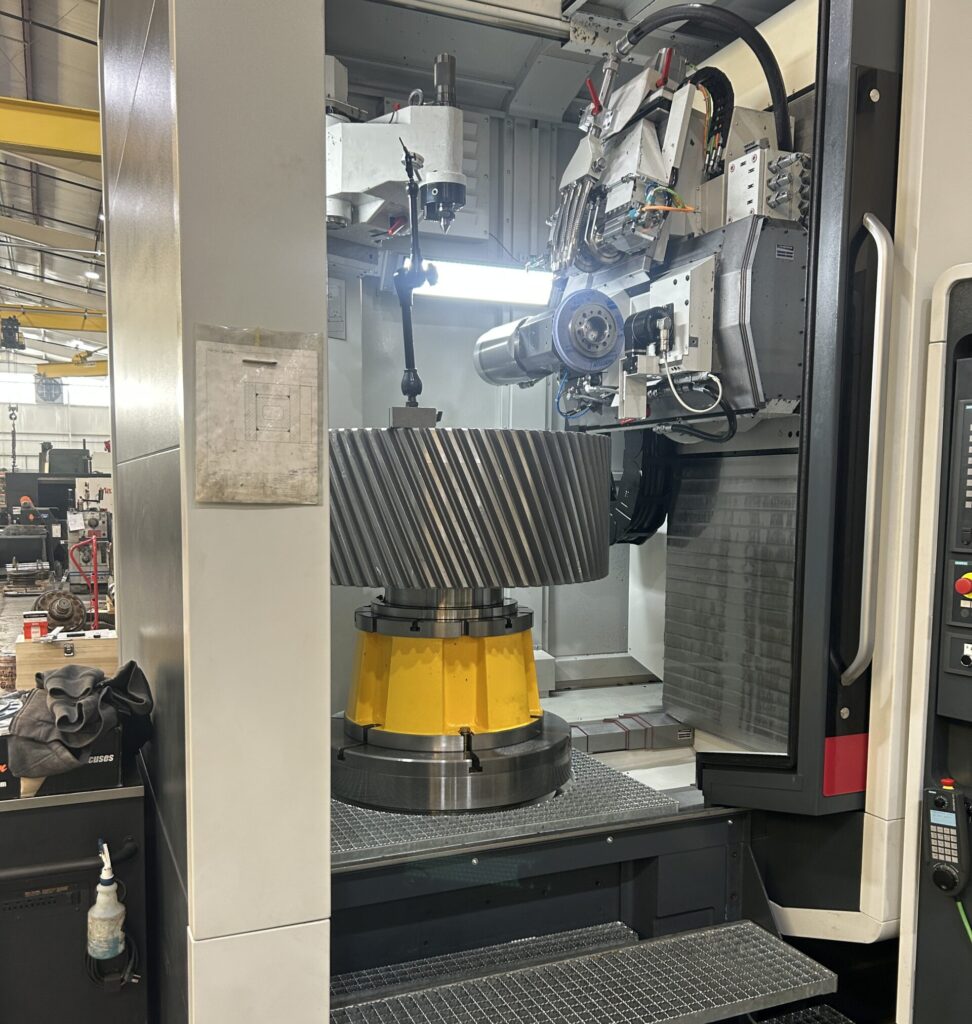
workpiece length of 1,545 mm
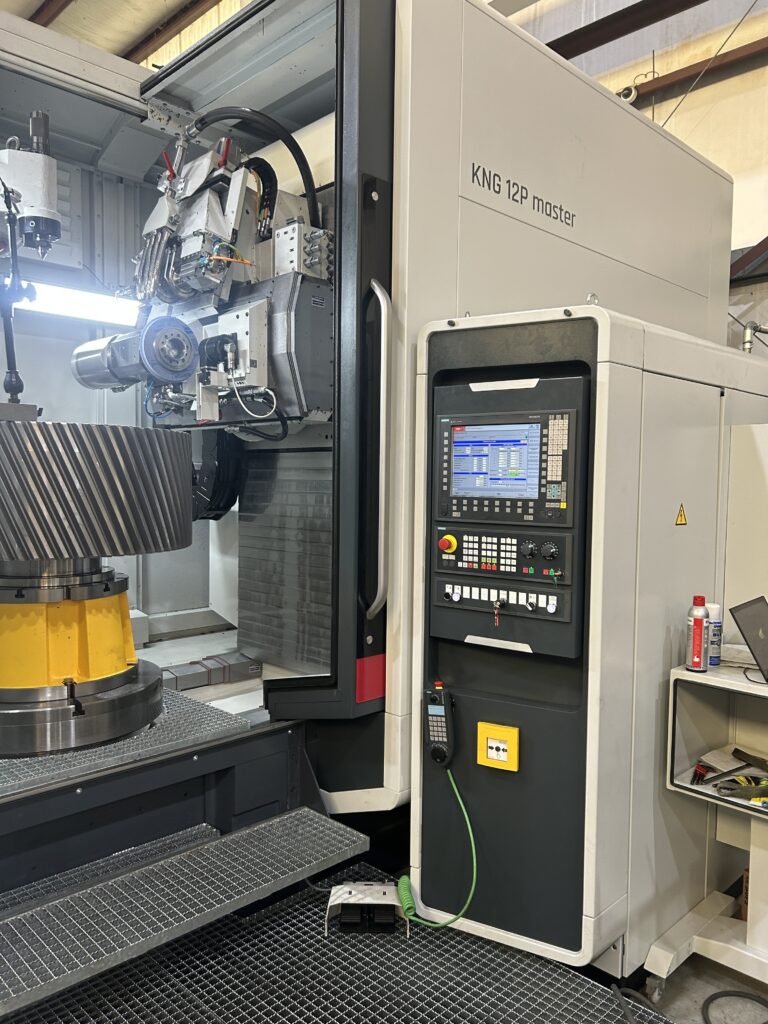
12,000 mm per minute
As anyone who’s ever dealt with a failed gearbox knows, even the slightest weakness or flaw in a gear can eventually cause a failure. By producing our own gears, we can assure you of the highest quality gears possible, up to AGMA Class 15 — the highest level recognized by the American Gear Manufacturers Association. Producing gears in-house is part of our overall commitment to vertical integration to ensure quality throughout our operation. All together, these new gear grinders give us the ability to manufacture high-quality, high-precision gears up to 94.5” in diameter to meet our customers’ varied needs.
In keeping with our commitment to quality, we also added two new heavy-duty, high-precision CNC Mazak lathes for a total of four. The two newest offer shorter lead times due to their very large motors and using programming based on 3-D models developed by our engineers.
Of note is the amazing Mazak QT350 CNC lathe, which has a multi-tasking configuration that enhances efficiency and reduces setup time by allowing for both turning and milling operations in a single setup.
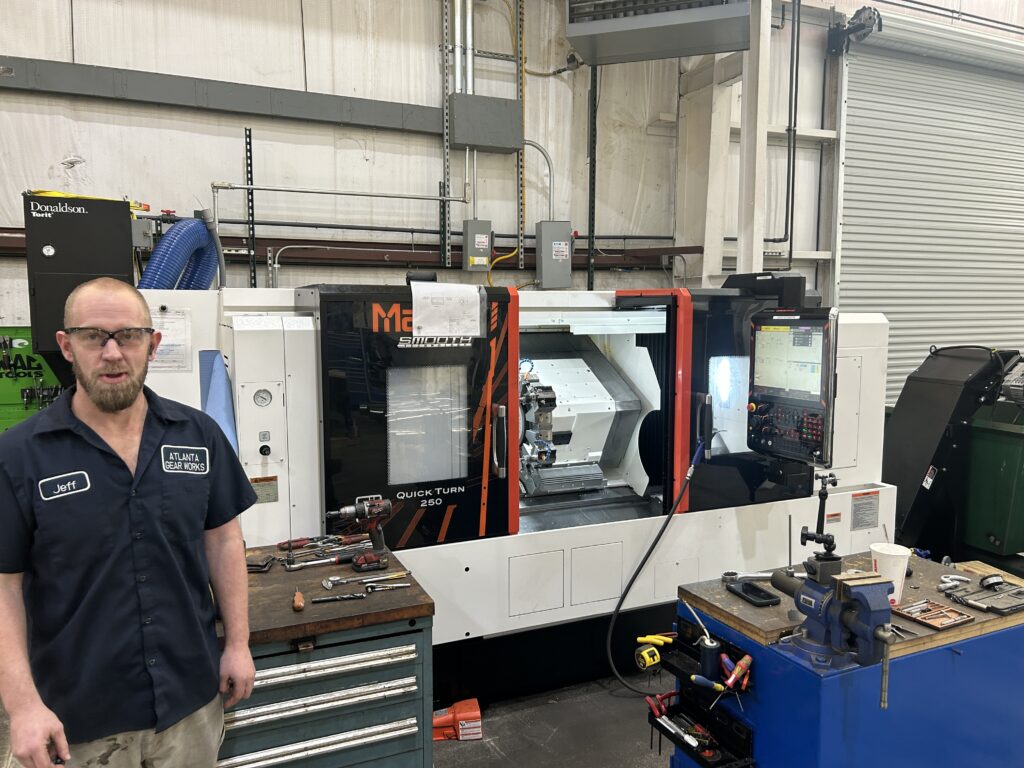
improve part roundness and surface finish.
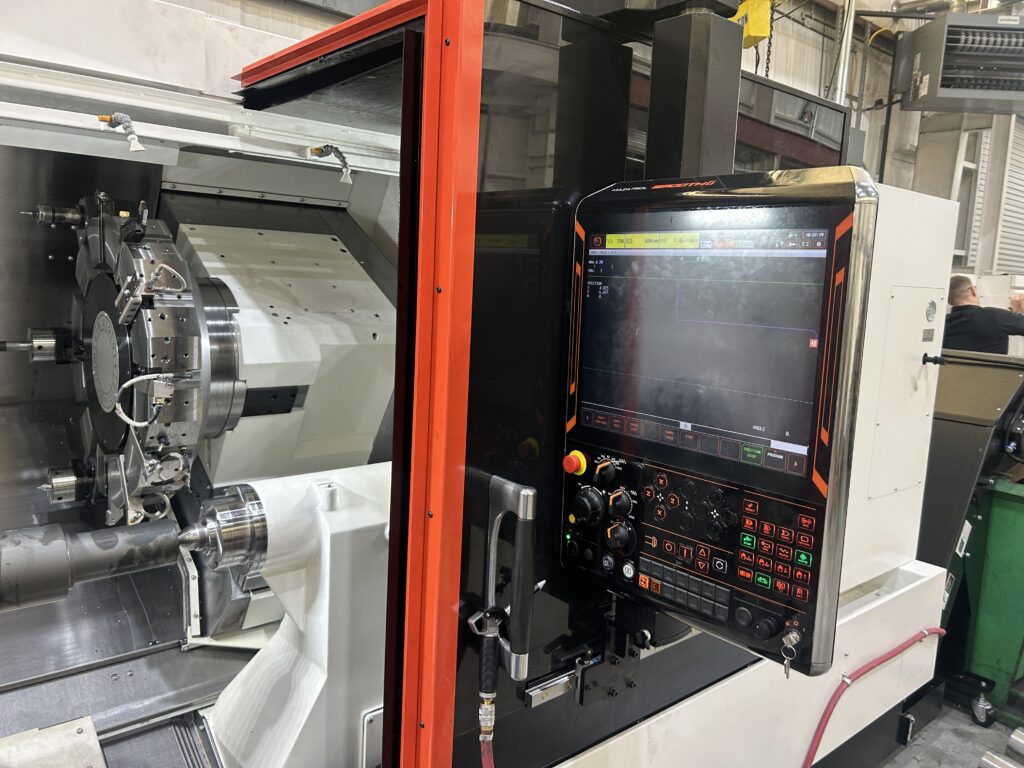
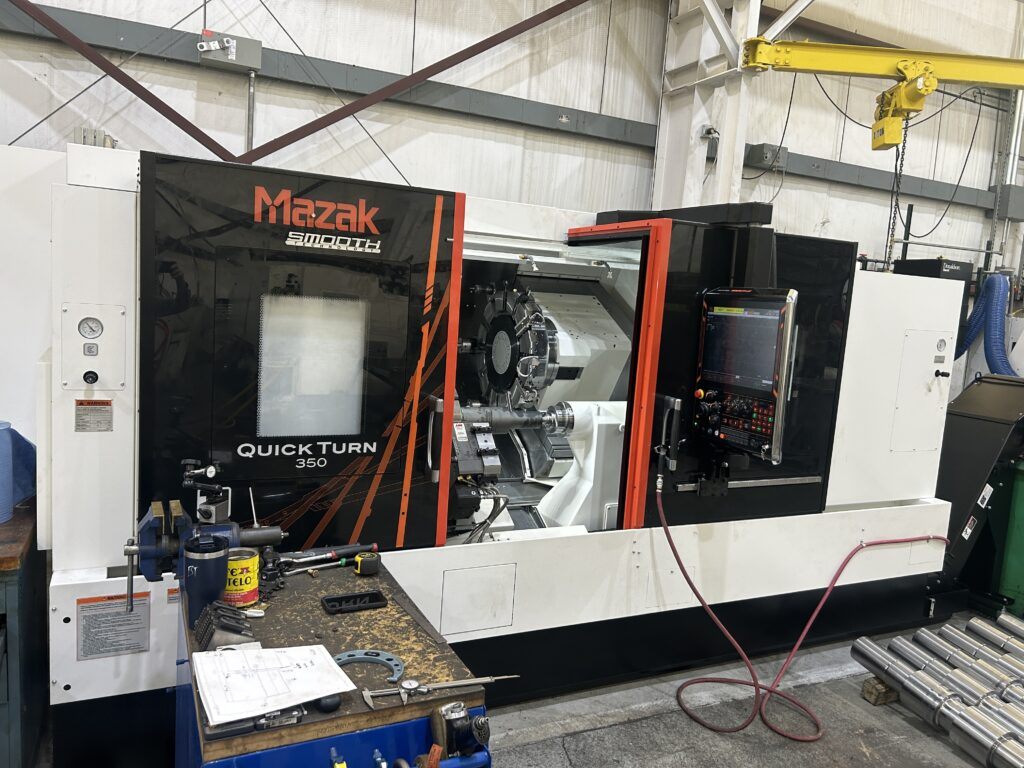
operations in a single setup.
These are but a few of the state-of-the-art machines we’ve invested in to perform repairs and rebuilds better, faster and more efficiently.
To get a full picture of the machines in our shop, please go here.
And to ensure we continue to deliver the same high quality you depend on, we’ve also added two gearbox assembly workstations to our assembly shop, for a total of 10.
Our peerless people.
But all of these investments would mean nothing without the talented, committed machinists, mechanics and engineers who know how to design for, program and use them. Even more, our people know the importance of the work they do in keeping our country’s top manufacturers up and running. It’s not easy to find them. When we do, we hire them.
Fortunately, after a yearlong national recruitment campaign, we found the kind of peerless people we seek and have added a second shift to our machine shop.
We also continue to offer ongoing training to everyone in the company. As a result, for eight continuous years, we’ve maintained our Timken Platinum certification, the highest certification awarded for gearbox repair and rebuilding practices.
But we’re not finished yet.
“We’re still a work in progress,” said Massa.