Not long ago, we performed a scheduled annual inspection at a paper mill. No one expected anything out of the ordinary. But we found a bearing on a paper machine in failure mode with the potential of causing the mill many weeks of downtime and the loss of millions of dollars in production.
Luckily, instead of the typical 24-week lead time, we had a replacement component already built and ready to go from stock. We installed it and prevented an imminent catastrophic failure — in just 2 days.
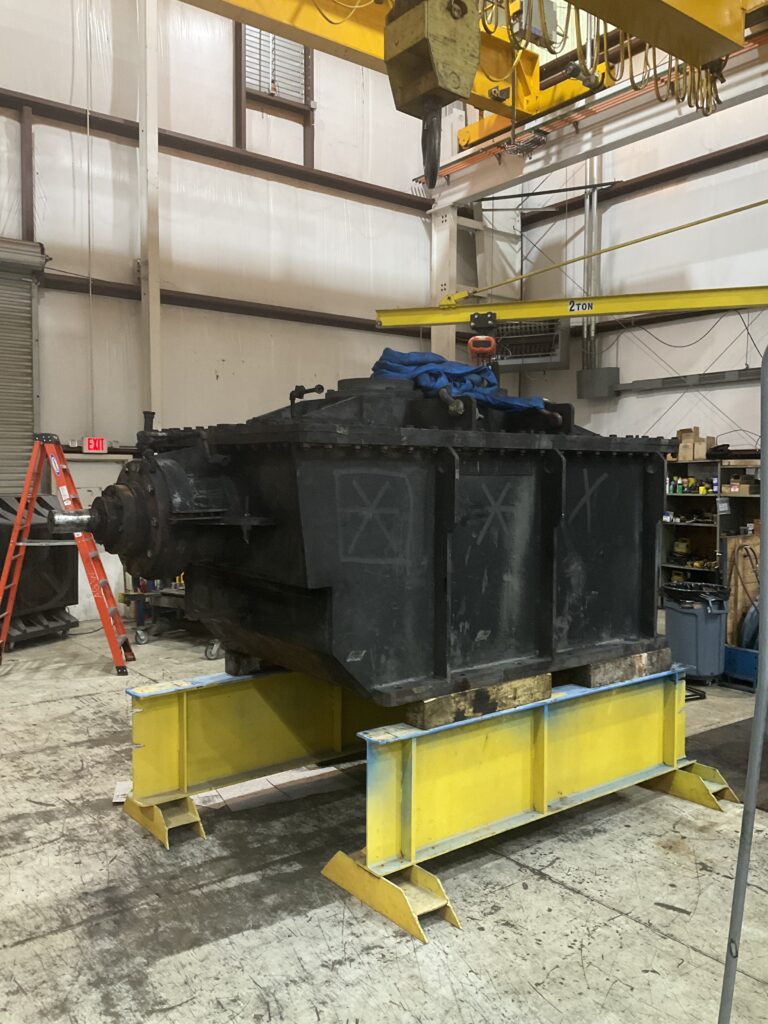
Paper mills in particular normally shut down for 7 to 10 days for annual maintenance. Gearbox maintenance is an essential part of the process, and our technical team is usually on site for 3 to 5 of those days.
Many mills also have one-day maintenance outages, usually lasting 12-hours at most. Despite the short amount of time involved, many mills include a gearbox inspection on their down day. Such was a recent case with a steel mill.
During the inspection, we found a bearing and gearing in failure mode on a 37,000-pound gearbox. A permanent repair required replacement of the gearing, which was obviously not possible within a single-day timeframe. But doing nothing would have likely led to a devasting failure causing many days
if not weeks of downtime.
We never give up.
In the time allotted, we provided a temporary solution by replacing the bearings and hand dressing the gears to enable them to last until a scheduled extended annual outage a few months away.
And we weren’t finished.
From old gear samples, our engineers reverse-engineered the gearing and our shop manufactured a replacement ahead of the mill’s upcoming planned annual outage. On the first day of the outage, the mill pulled the gearbox and transported it to us. We were ready and waiting. We rebuilt it and shipped it back within 5 days for reinstallation. Problem solved. Unplanned downtime avoided.
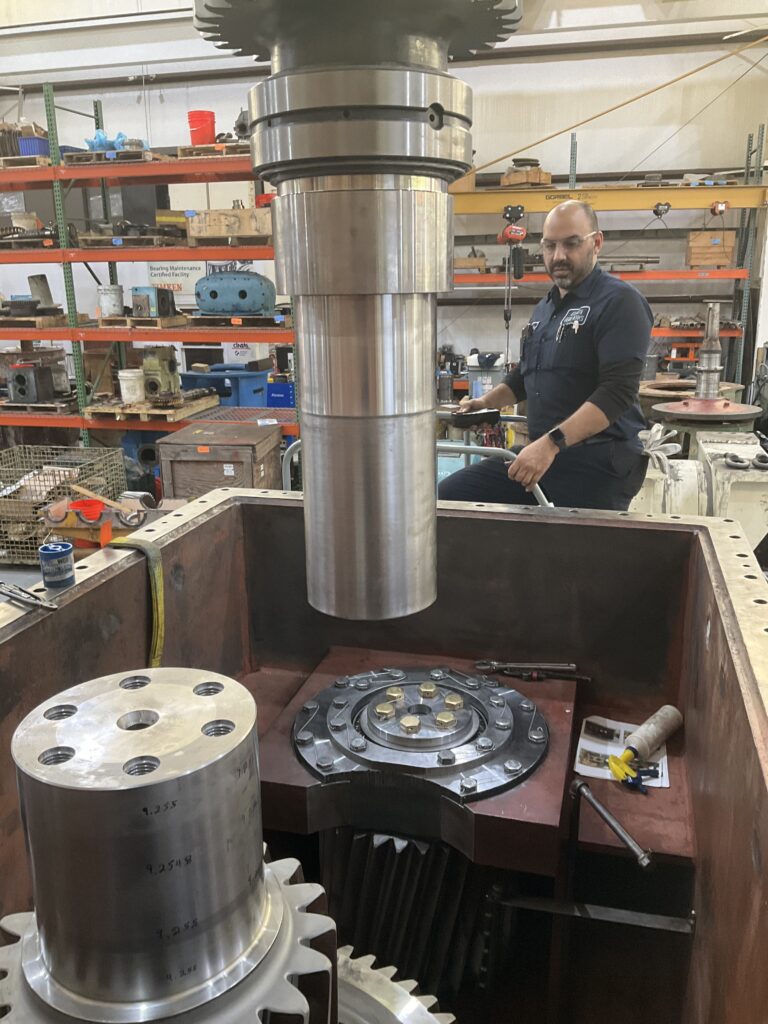
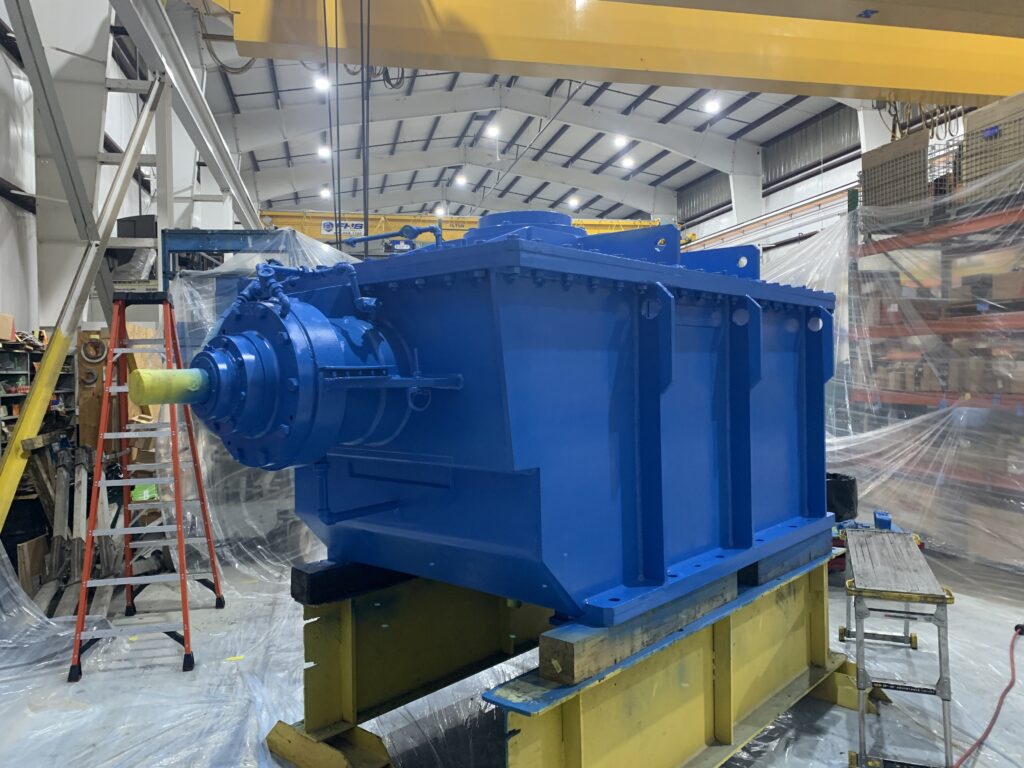
Gearbox inspections solve problems.
Our maintenance inspection teams range from one to 20 people depending on the size and complexity of the job. A typical team can include technical reps, mechanics and even an engineer when an on-site rebuild is called for. More than just diagnosticians, they are first and foremost problem-solvers.
The fact is they not only detect problems. They also fix them — sometimes right on the spot. Thanks to our extensive field services and in-house vertical integration, we have the expertise and resources to do whatever is necessary to make the most of our customers’ planned downtime to get them up and running as quickly as possible.
If you haven’t made an Atlanta Gear Works gearbox maintenance inspection part of your next planned maintenance, either routine or annual, we’d be honored to join you. Our inspection teams are always in demand, so please contact us to schedule your time asap at either.